one of us
| I tend to use as low a pressure I can get and still be productive around 20 psi. The glass beads I have are called 80 grit whatever that means. I think they are typically classified by sieve size. Make sure the beads are fresh and round not fractured or they will make a rough finish like sand blasting. |
| |
one of us
| AC works well at 30-40psi. About like a factory Rem or Win SS.
MtnHtr |
| |
one of us
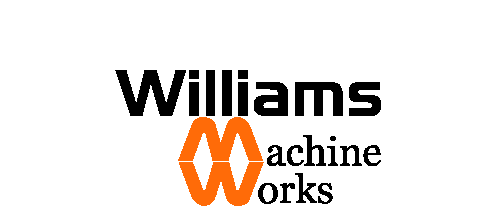
| Quote:
AC works well at 30-40psi. About like a factory Rem or Win SS.
MtnHtr
MtnHtr is on the right track here. The brand name is Potters and the grit is indeed AC to match what USRAC is using, but pressures are typically ran at 100 psi for most applications. Helps the beads flow a little better. This is how we blast the trigger guards that are used on USRAC'S stainless sporters, as well as all of our other parts, whether they be steel or stainless. |
| Posts: 1021 | Location: Prineville, OR 97754 | Registered: 14 July 2002 | 
IP
|
|
One of Us
| Any reason why you can't hit the action at the same time to make sure it matches?
BTW, grit size is based on a sieve used to grade the paticles. The sieves have fine wire and an 980 grit is 80 openings to the inch. In my former life as a civil engineer/ materials engineer my lab did a lot of gradations but mainly on roadway materials. The sieves we used went to to 200. The gradations on sandpaper are the from the same thing. |
| Posts: 4917 | Location: Wenatchee, WA, USA | Registered: 17 December 2001 | 
IP
|
|
one of us
| The nozzle opening at the end of the gun will have a great effect also. Mine is a gravity fed to a syphon tube. Start @ low psi and work your way up. Another thing to remember is I'm stating the pressure with the nozzle on or blasting. Big difference between static pressure with everything off and operating pressure especially if you have a small regulator. With my setup 80 - 100 psi will definately fracture the beads and the appearance will suffer greatly and be much coarser than Remington or Winchester. If you are using a pressurized feed where the hopper is pressurized. Its a different story altogether you can set the pressure upwards of 100 psi and by adjusting the bypass valve ( thus decreasing operation pressure at the nozzle ) that feeds air to the nozzle you can get a fine finish with the higher pressure setting. Bottom line the lower the velocity of the sphere the less the metal is displaced and the smoother the finish. The lower the operating pressure, the easier it is for the compressor to keep up. Using a smaller nozzle helps decrease air demand and raises velocity. At the end is a link to potters for sieve size conversions, potters uses their own system. I would have AB size and when I'm finished I end up with a smooth ( doesn't hold dirt ) less reflective finish than supplied by Remington or Winchester, which is what I prefer. www.pottersbeads.com/Literature/HiIndex--BallotiniBeads.pdf |
| |
one of us
| Scrollcutter, I suspect micrometers to be done differently. I have thought about trying soda blasting to just dull a finish and not make the peen marks. Its used by the auto restoration crowd to remove paint as its less prone to warping sheetmetal. The results seem similar but I'm unfamilar with the rest other than the equipment being a pressure feed system. Its essentially baking soda granulated for that purpose. A couple of boxes of Arm&Hammer won't break the bank to try. I'd start with a small nozzle and high pressure and do a sample. Let me know how it works. |
| |